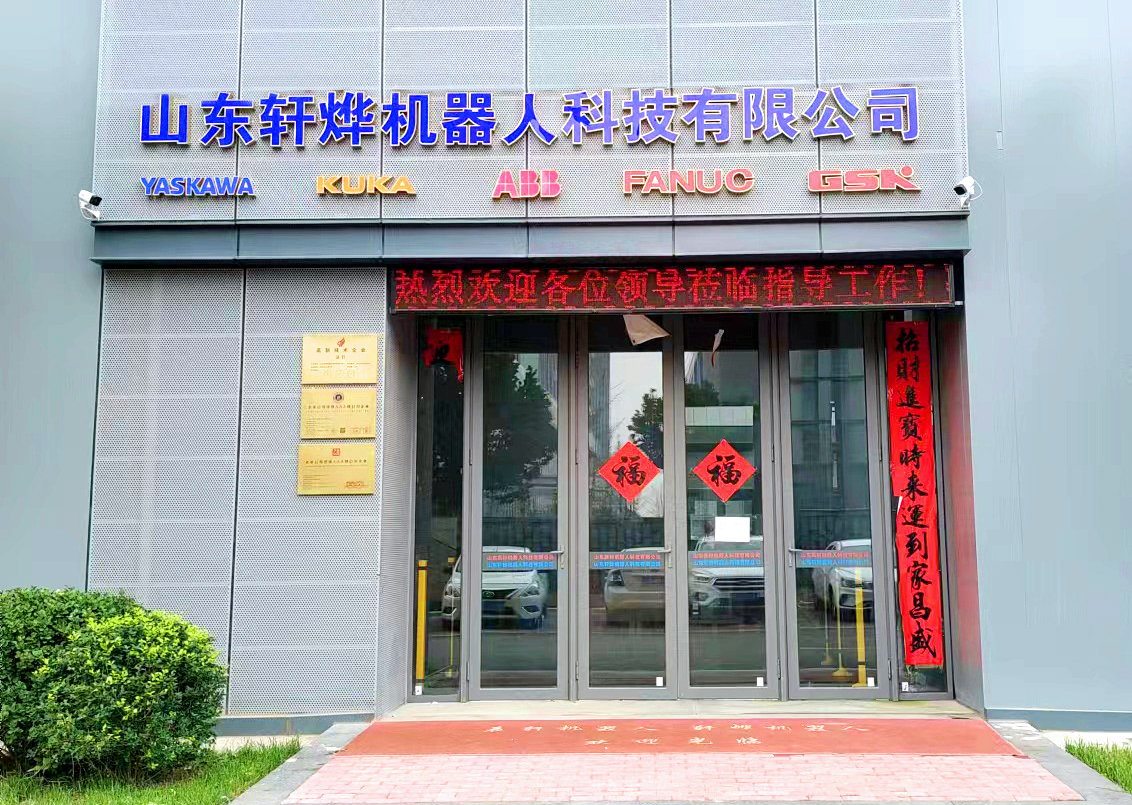
山东轩烨机器人科技有限公司是一家以工业机器人以及自动化非标设备于一体的技术企业,公司致力于焊接、切割、机器人机床上下料等领域的机器人智能化研究和产业化应用
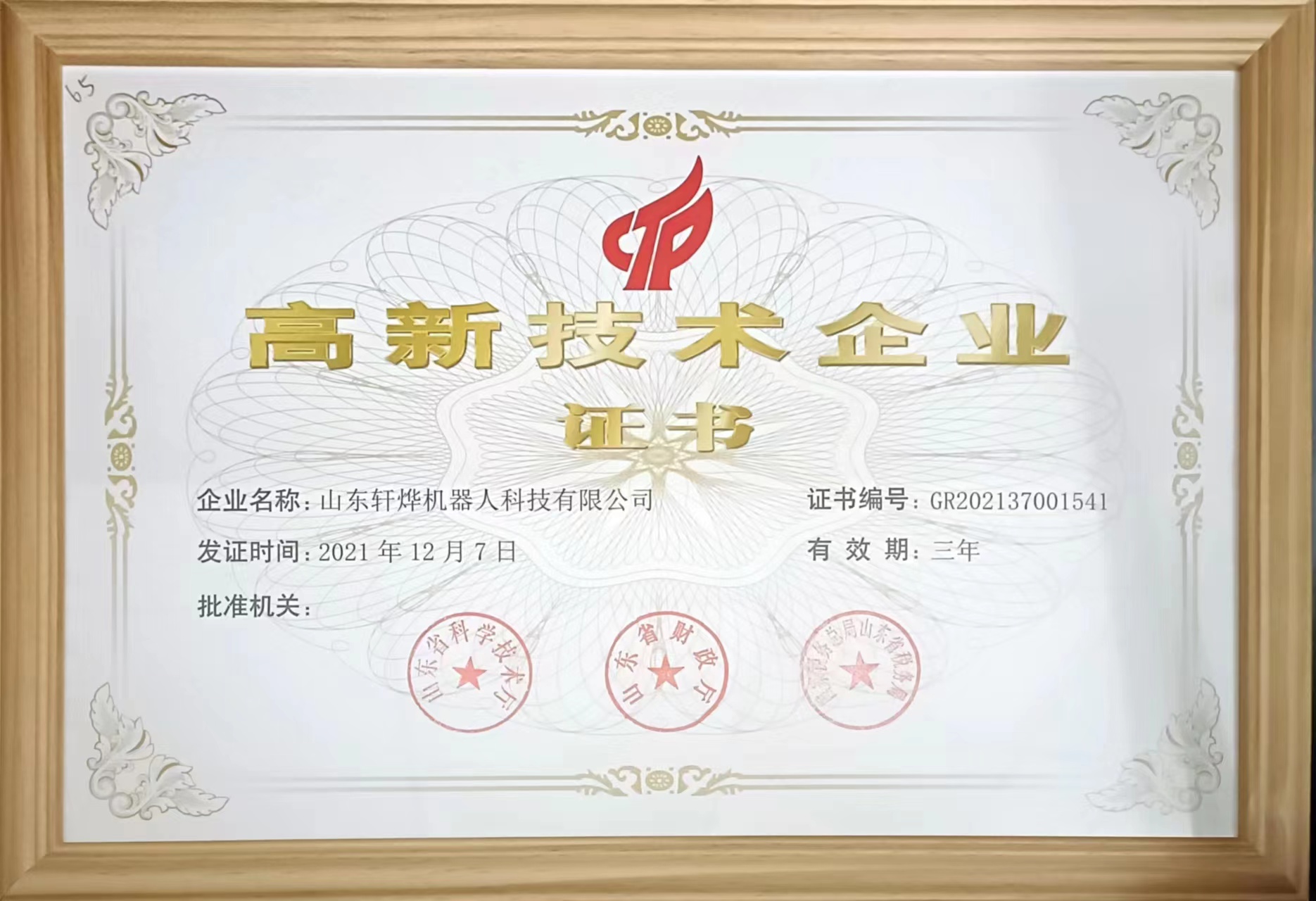
公司立足于高端装备制造等战略新兴产业,将追逐“制造2025"致力于机器人技术和互联网技术的深度融合,推动智造。
发布:2024-01-02 浏览:0
铝合金自动焊接机械手是在准平面、空间狭窄的环境下工作,为了机器人能根据电弧传感器的偏差信息,跟踪焊缝自动焊接,要求所设计的机器人应该结构紧凑、移动灵活且工作稳定,为了减少恶劣焊接环境下粉尘对运动部件影响,采用全封闭式结构。
The aluminum alloy automatic welding robot operates in a quasi flat and narrow space environment. In order for the robot to track weld seam automatic welding based on the deviation information of the arc sensor, it is required that the designed robot should have a compact structure, flexible movement, and stable operation. In order to reduce the impact of dust on moving parts in harsh welding environments, a fully enclosed structure is adopted.
铝合金自动焊接机械手现在被广泛的应用,其中汽车生产企业使用铝合金自动焊接机械手很多,使用铝合金自动焊接机械手在很大的程度上提高了产品的质量。
Aluminum alloy automatic welding robots are now widely used, among which many automobile production enterprises use aluminum alloy automatic welding robots. The use of aluminum alloy automatic welding robots greatly improves the quality of products.
人工焊接是一项非常繁重的工作,随着焊接要求越来越高,一般的人工难以胜任,焊接时的火花和烟雾对人体有伤害,使焊接工人也越来越少,所以使用机器人焊接解决了企业用工的难题。为了减少焊接过程中出现残渣,需要事先对铝材经进行清理工作,工件焊口及焊丝表面的膜和油污杂质,在焊接过程中会产生高温环境,铝材在加热呈现液态状态的时候流动性较高,这就需要采用工装夹具对铝材工件进行夹紧,减少工件的变形。
Manual welding is a very heavy job. With the increasing requirements for welding, ordinary manual workers are unable to handle it. Sparks and smoke during welding can cause harm to the human body, resulting in fewer and fewer welding workers. Therefore, the use of robot welding has solved the problem of employment in enterprises. In order to reduce residue during the welding process, it is necessary to clean the aluminum material in advance. The film and oil impurities on the welding joint and wire surface of the workpiece will generate a high-temperature environment during the welding process. When the aluminum material is heated to a liquid state, its fluidity is high. Therefore, it is necessary to use fixtures to clamp the aluminum workpiece and reduce its deformation.
为了稳定焊接工作,需要按照合理的顺序进行编程并根据待焊工件进行调试,给弧焊机器人编程的时候,要选择合理的焊接顺序,一般都是以减小焊接变形、焊枪行走路径长度来制定焊接顺序。操作人员按照正确的流程进行机操作,焊接机器人在焊接铝材的过程中性能稳定,提高焊接效率的同时稳定焊接质量,提高生产效益。
In order to stabilize welding work, it is necessary to program in a reasonable order and debug according to the workpiece to be welded. When programming the arc welding robot, a reasonable welding sequence should be selected, usually to reduce welding deformation and the length of the welding gun walking path to formulate the welding sequence. Operators operate the machine according to the correct process, and the welding robot has stable performance during the welding of aluminum materials, improving welding efficiency while stabilizing welding quality and improving production efficiency.
焊后留在焊缝及附近的残存焊剂和焊渣等不仅会影响后续的工作,还会破坏铝材表面的的钝化膜,有时还会腐蚀铝件,应清理干净,操作人员需要对焊接机器人进行维护保养,后续工作的稳定性。
The residual flux and slag left in the weld seam and its vicinity after welding not only affect subsequent work, but also damage the passivation film on the surface of the aluminum material, and sometimes corrode the aluminum parts. They should be cleaned thoroughly, and operators need to maintain the welding robot to ensure the stability of subsequent work.
使用铝合金自动焊接机械手焊接要满足的条件是:
The conditions that need to be met when using an aluminum alloy automatic welding robot for welding are:
一、机器人对整体尺寸精度要求不是特别高,铝合金自动焊接机械手都有偏差传感以及焊接过程中的电弧跟踪功能,所以可以进行纠正。
1、 Robots do not have particularly high requirements for overall dimensional accuracy. Aluminum alloy automatic welding robots all have deviation sensing and arc tracking functions during the welding process, so they can be corrected.
二、对接焊缝的根部间隙要稳定均匀,现在的铝合金自动焊接机械手一般有间隙传感功能,在程度内可以根据实际的焊缝根部间隙进行参数补偿,但是如果波动太大,间隙太不均匀的话,焊缝熔合和焊缝成型质量也会很不稳定。
2、 The root gap of the butt weld should be stable and uniform. Nowadays, aluminum alloy automatic welding robots generally have gap sensing function, which can compensate for parameters based on the actual root gap of the weld to a certain extent. However, if the fluctuation is too large and the gap is too uneven, the fusion and forming quality of the weld will also be very unstable.
三、角焊缝的拼装间隙要控制,否则容易焊穿,在有间隙的地方,机器人进行焊接前进行预先的人工打底可以减少焊穿的发生。
3、 The assembly gap of the fillet weld should be controlled, otherwise it is easy to weld through. In areas with gaps, pre manual bottoming by robots before welding can reduce the occurrence of weld through.
四、焊缝的焊接余量需控制,比如角焊缝要求10,实际板边焊接余量只有8,那肯定会咬边。
4、 The welding allowance of the weld seam needs to be controlled, for example, if a fillet weld requires 10, but the actual plate edge welding allowance is only 8, it will definitely cause undercutting.
感谢您的阅读,此文的文章来源:焊接机器人更多的内容和问题请点击:http://www.xuanyerobot.com我们会继续努力的为您提供服务,感谢您的支持!
Thank you for reading. The source of this article is welding robots. For more information and questions, please click: http://www.xuanyerobot.com We will continue to work hard to provide you with services. Thank you for your support!
截屏,微信识别二维码